Training, preventive maintenance, awareness-raising on the use of tools, support for sales staff, and project managers upstream – all these activities are of crucial importance in maintaining and ensuring the maximum safety of DEFINOX valves.
We spoke to Hervé Richard, Customer Service Manager at DEFINOX and the person responsible for these activities.
First of all, can you tell us about your role within DEFINOX?
As Customer Service Manager at DEFINOX since 2017, my fields of action are diverse and varied, but all converge towards helping customers use our valves.
I’m involved not only in answering customers’ questions, but also in three other areas: preventive maintenance, the management of non-conformities and, lastly, training. These three subjects are directly linked to the safe use and maintenance of our equipment.
DEFINOX is renowned for the quality of its valves, which are 100% maintainable.
However, it is our responsibility to ensure the safety of people throughout the processes, from installation to dismantling of our powerful valves and actuators. DEFINOX is renowned for the quality of its valves, which are 100% maintainable. As a result, we pay particular attention to the education and training of the users of our valves.
What measures has DEFINOX put in place to ensure safe operations on the customer’s premises?
DEFINOX places the utmost importance on safety. It is integrated into the design of the valve and throughout the assembly and maintenance phases.
In the event of a maintenance requirement, our after-sales technicians will only intervene once they have received the prevention plan duly completed by the customer. This plan specifies essential information such as the environments, the risks involved and the equipment on site. The customer’s signature on this prevention plan attests to the safe feasibility of the intervention by a DEFINOX technician.
We have the right equipment to handle risky areas. In addition to the tool cases and the press, we have handling systems to extract valves that are difficult to access, in complete safety for our teams and line operators. Specifically, an electrical device has been installed to effortlessly manoeuvre the press, which can weigh up to 130 kg. The aim of this initiative is to eliminate dependence on the customer for loading and unloading the press from the truck. Nothing is left to chance.
You mentioned that DEFINOX valves are designed with safety in mind. What safety features are built into the products?
In addition to the precautions mentioned above, our DEFINOX products incorporate tried and tested safety systems:
- in the event of pressure in the line, bayonet fixing on the pigging stations ensures safe removal.
- the clamp collars used on pigging systems are fitted with pig presence sensors.
- VEOX non-mixing valves incorporate a protective lantern housing as standard.
We automatically provide instructions and guides for the safe handling of the various DEFINOX tools, explaining the importance of assembly and disassembly procedures.
Customers also have access to numerous video resources on our websites, our YouTube channel, and the “DEFINOX id” augmented reality application. These guides detail, step by step, the dismantling sequences, the replacement of wearing parts, and the reassembly of the valves and pigging systems.
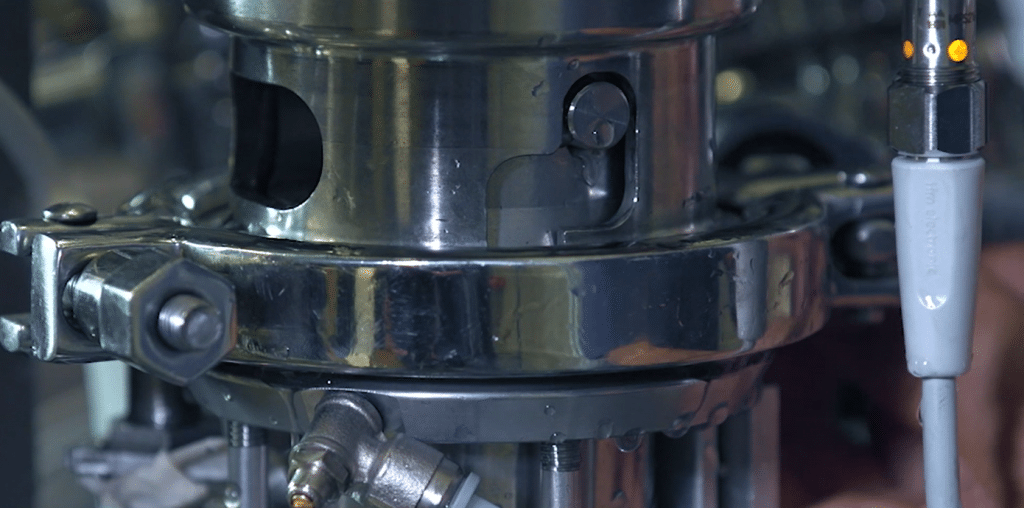
Our sales staff and project managers provide support prior to installation, enabling us to anticipate the customer’s needs, both in terms of tools and training.
Concerning the Qualiopi certification you recently obtained, how does this represent a guarantee of quality and a benchmark for DEFINOX?
Qualiopi certification is a mark of quality for our customers, entailing a complete overhaul of our training process.
This certification requires us to continually adapt to the needs of our users, including enriching our teaching content, accommodating people with disabilities, developing new materials to make them easier to read, and adapting quickly to satisfy our customers. We also include and monitor our trainers in this process.
Our training offer, which can be adapted to suit the type of valve and the issues identified, can be given on the customer’s site or at DEFINOX.
Environmental issues and the 100% maintainable nature of our valves are directly linked, encouraging DEFINOX to help its customers understand how the equipment works.
Although all the training methods can be provided on the DEFINOX site in a specially-equipped training room with all the necessary equipment, we had to be flexible.
The particular health situation in 2020 has prompted us to adapt our processes by introducing maintenance videos, remote video-conferencing training sessions, and by strengthening our team with bilingual trainers, to continue our international training module.
Together with the design office, we continue to pay close attention to feedback from the field to improve the safety of our products and our information media.
To sum up, at DEFINOX we are committed to a process of constant improvement to guarantee safety in line with changes in the field.
The post DEFINOX, safety at the heart of the customer process appeared first on Definox EN.